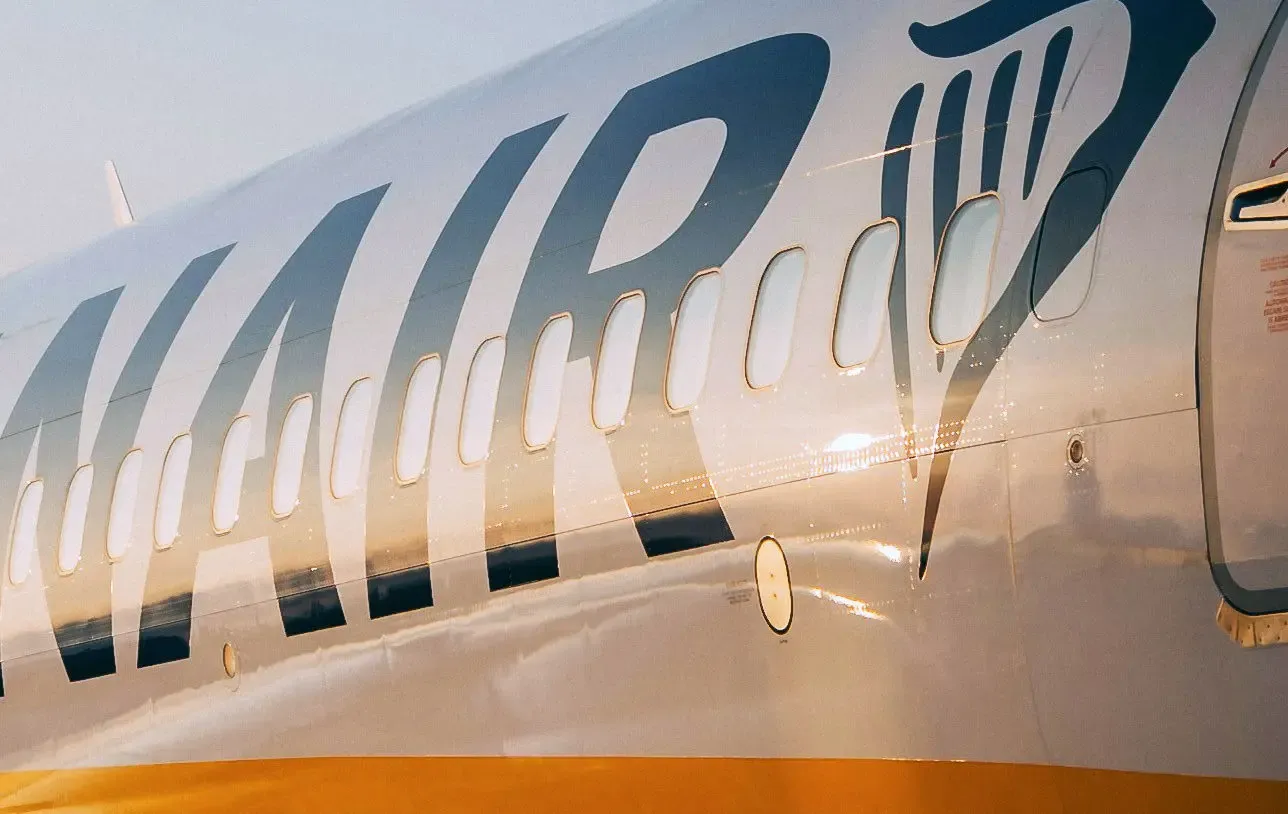
The Engineering Behind: Why Planes Use Rivets
Planes are riveted and not welded due to the structural integrity and flexibility that rivets provide. Learn more about why riveting is the preferred method for aircraft construction.
Table of Contents
Modern aircraft are filled with advanced technology. Engineers have made significant advancements in avionics, aerodynamics, safety systems, and material science. Despite these advancements, modern aircraft are still constructed using rivets, a relatively old form of mechanical fastening known for shipbuilding and bridge construction.
So why do airplanes, with all the technological advancements, still rely on the seemingly ancient method of using rivets in their construction?
The use of rivets in aviation is deeply rooted in science and engineering principles that ensure safety, durability, and efficiency.
Let's explore why planes use rivets and how this age-old technique remains relevant in aircraft manufacturing.
Understanding Some Basics of Aircraft Construction
In the intricate world of aircraft construction, selecting materials and assembly methods that can endure the rigors of flight is paramount. The bulk of an aircraft's structure is composed of aluminum alloys, celebrated for their blend of lightness and strength. Aircraft materials are pivotal in achieving aviation's performance and safety standards. However, the process of joining these pieces presents a unique set of challenges. This is where the role of rivets becomes indispensable.
Riveting creates a robust and permanent bond between metal components without compromising the metal's inherent properties. Unlike welding, which subjects metals to high temperatures that can alter and weaken aluminum's structural integrity, riveting connects pieces mechanically. This technique involves the insertion and deformation of the rivet, clamping the metal parts firmly together. This method not only preserves the strength of the aluminum alloys but also ensures that the assembled structure can withstand the stresses and strains of flight. In addition, welding aluminum is not as straightforward as welding steel. Steel has a broader temperature range where it becomes increasingly soft. Aluminum alloys, on the other hand, transition from a solid to a liquid state in a matter of a few degrees.
Another essential factor is that riveted constructions are easier to inspect, maintain, and repair. Inspections and aircraft repairs often involve taking things apart and replacing them, which is much easier with riveted constructions than with welded constructions.
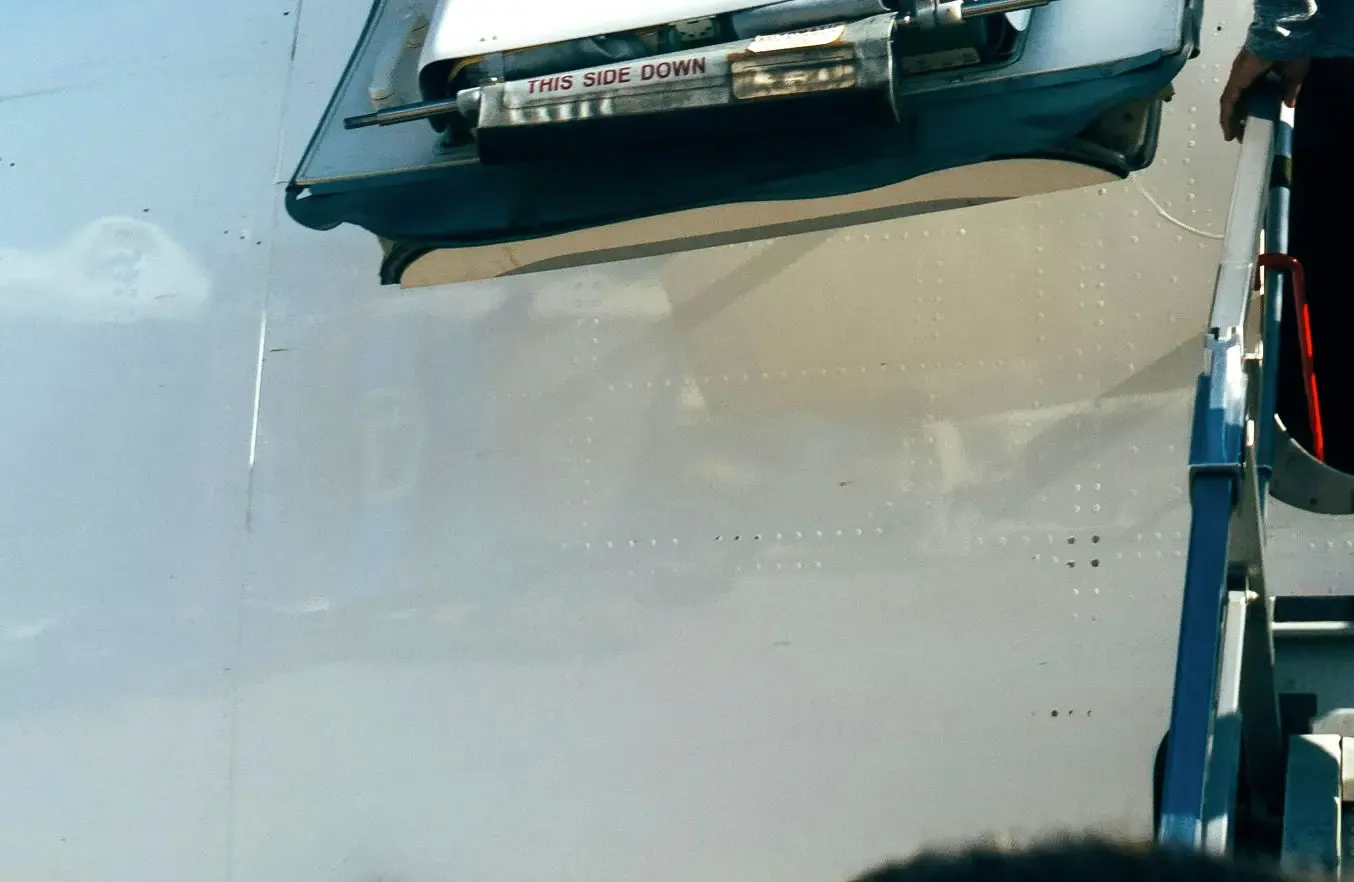
The choice of riveting in aircraft assembly is also influenced by the need for precision and reliability. Each rivet inserted is a point of strength, meticulously placed to contribute to the overall integrity of the aircraft. In an industry where every detail counts, rivets' proven effectiveness in maintaining structural cohesion is invaluable. As aircraft design evolves, the fundamental principles of selecting robust materials and reliable assembly techniques remain central, with riveting as a critical player in the construction process.
The Rivet's Role in Durability and Strength
Rivets are essential in maintaining airplanes' structural integrity, which is vital to the craft's overall durability and strength. They function by evenly dispersing stress across the aircraft's metal surface. This is crucial because it prevents stress from accumulating in any single area, which could lead to the material weakening or failing under the pressures of flight. By distributing the forces exerted on the plane, rivets help mitigate potential damage and extend the aircraft's lifespan.
Furthermore, the mechanical bond created by rivets is incredibly robust, enabling the joined metal parts to endure the extreme forces encountered at high speeds and altitudes. This bond is especially critical during turbulent conditions or when the aircraft undergoes sudden maneuvers, where the strength of each component is tested. The riveted connections are more fatigue-resistant. Welded joints are more likely to develop cracks under continuous load cycles. That is an essential characteristic given the cyclical loading and unloading of stresses that airplanes experience throughout their operational life.
Another critical advantage of rivets is their ability to secure pieces of metal together in a firm but flexible way to accommodate slight movements. This flexibility is vital for the longevity and safety of the aircraft, ensuring that the structural components can tolerate the rigors of flight without succumbing to brittle fractures or other forms of mechanical failure.
In essence, rivets provide a better balance of strength, durability, and resilience that is unmatched by other fastening methods, solidifying their status as an integral part of aircraft design and construction.
Adaptability to Thermal Expansion and Contraction
One of the lesser-known yet critical challenges airplanes face is dealing with the vast temperature changes encountered during flight. From the biting cold of high-altitude environments to the warmth on the ground in some parts of the world, these shifts can have profound effects on the materials that make up an aircraft.
This is where rivets' adaptability to thermal expansion and contraction plays a crucial role. Rivets, designed to securely fasten materials while allowing for minor movements, are well suited to accommodate the inevitable shifts in size and shape of aircraft components when temperatures fluctuate.
This dynamic adaptability ensures that, as metals expand or contract in response to temperature changes, the integrity of the aircraft's structure remains uncompromised. The slight give afforded by rivets prevents the buildup of stress that could lead to cracks or breaks in the aircraft's skin or structure, phenomena that rigid fastening methods might provoke under similar conditions.
Such flexibility is essential for maintaining the aircraft's resilience against the diverse thermal environments it traverses and ensuring its components' long-term durability.
Efficiency and Reliability of Riveting in Manufacturing
The methods chosen for assembly play a pivotal role in determining the final product's performance, reliability, and cost in aircraft construction.
Riveting, a method with a long history in aviation, stands out for its contribution to manufacturing efficiency and the dependable connections it forms. Unlike more technologically intensive joining methods, riveting can be executed quickly and does not necessitate complicated and extensive training for the workforce (although some experience is, of course, required.). This aspect significantly reduces the time and costs associated with the assembly of airplanes, marking riveting as a notably economical choice in aircraft manufacturing.
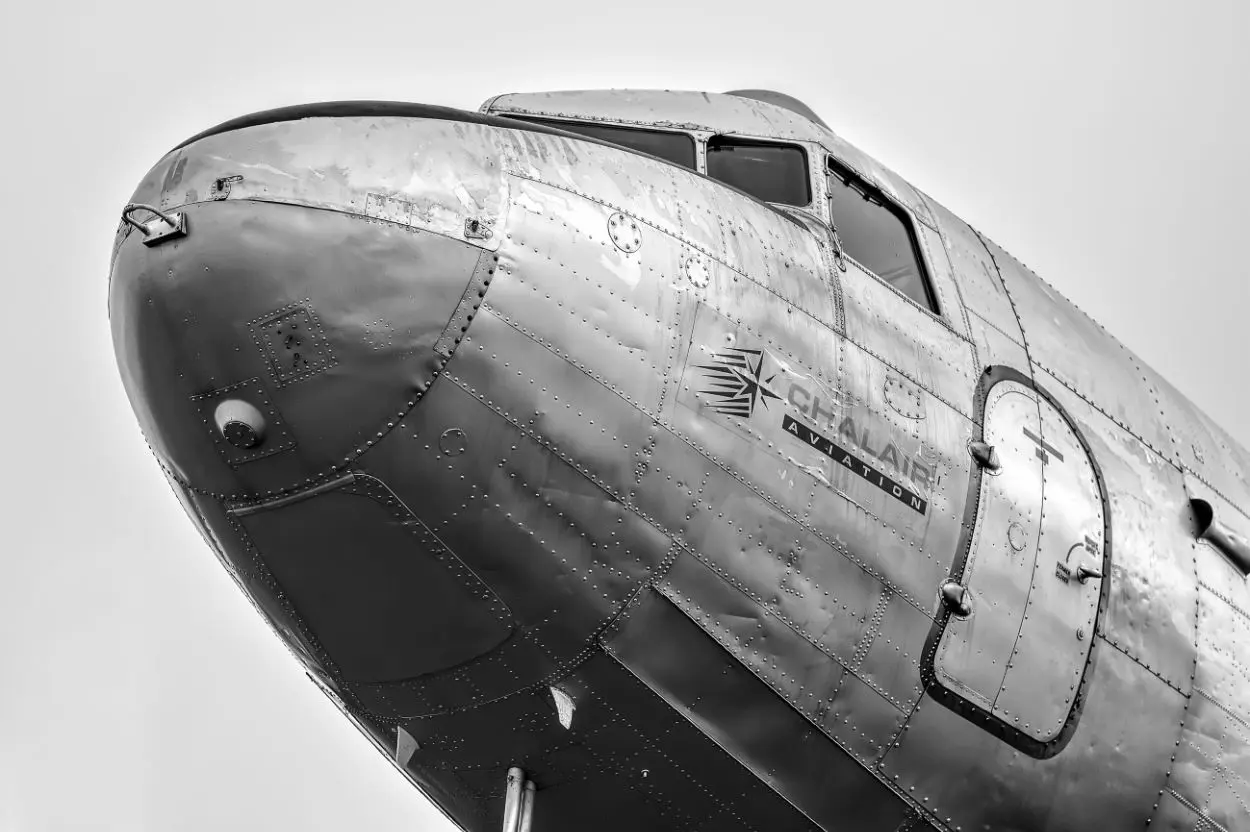
Moreover, riveted joints are exceptionally reliable. These connections are subject to visual inspection, which allows for straightforward monitoring and maintenance. This ease of inspection is invaluable, as it facilitates the early detection of potential issues, enhancing aviation safety measures. The ability to inspect riveted joints without the need for specialized equipment or techniques ensures that the integrity of the aircraft's structure can be confidently assessed throughout the aircraft's operational life.
Riveting's role in manufacturing is not just about connecting pieces of metal; it's about doing so resourcefully and securely. The method's blend of relative simplicity and effectiveness continues to make it a preferred choice in aircraft assembly.
The Evolution and Future of Rivets in Aviation
While other areas of aviation technology propel forward, the rivet (and the installation method) have not seen similar significant advancements since World War II.
However, some minor improvements to the aircraft rivet and how manufacturers install them have been made.
Innovations in the types of rivets, moving beyond aluminum to incorporate advanced alloys and even composite materials, have opened new avenues for aircraft design and construction. These modern rivets offer enhanced performance characteristics, including superior strength-to-weight ratios and increased resistance to corrosion, which are critical in the harsh operating environments encountered by aircraft.
The evolution of riveting technology extends to the tools and techniques employed in their installation. Automated riveting systems and precision tooling, have streamlined the assembly process, increasing efficiency and reducing the margin for error. These advancements have bolstered aircraft production rates and improved the consistency and reliability of riveted joints.
Despite the emergence of alternative joining techniques, such as adhesive bonding and laser welding, riveting remains a staple in aviation manufacturing. Its enduring presence is a testament to the balance it offers between mechanical strength, reliability, and ease of inspection and maintenance.
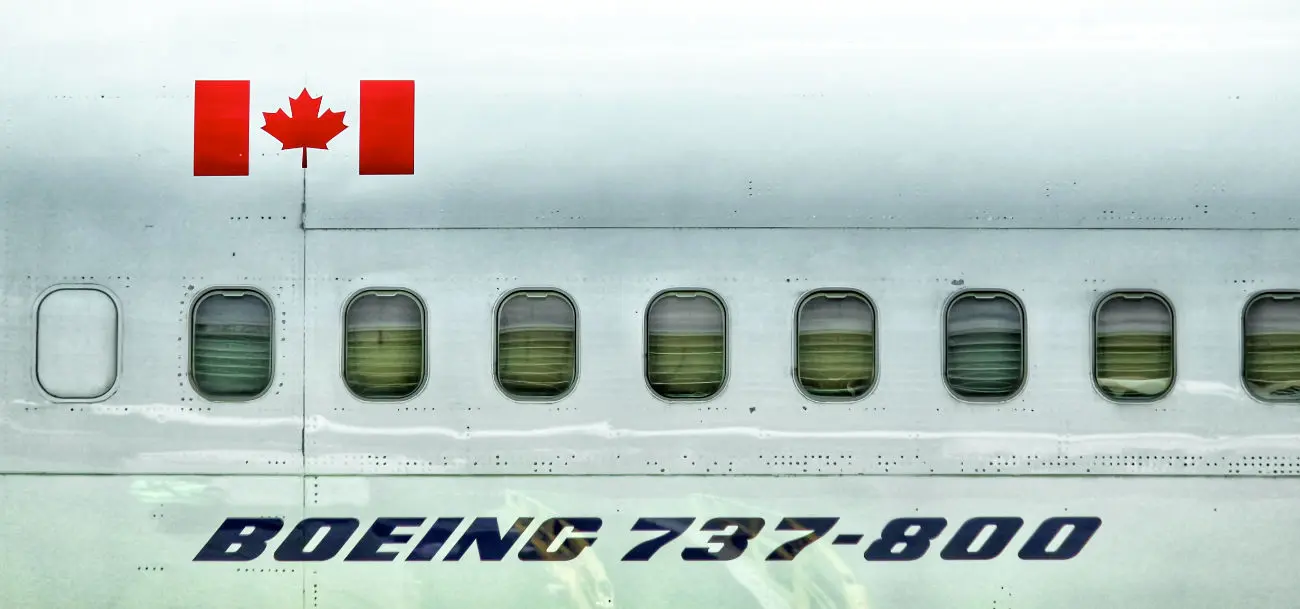
The ongoing development in riveting technologies suggests a future where these fasteners continue to adapt and thrive, ensuring their relevance in aviation's next chapters. As aircraft designs become increasingly complex and materials more sophisticated, the rivet's role is set to evolve, mirroring the industry's continuous quest for innovation and improvement.
That is also reflected in the numbers. Stratview Research expects the global market for aircraft rivets to reach $388.9 billion in 2028, constituting a compounded annual growth rate of 8.3% in the years 2023 to 2028.
According to Stratview Research, there are several reasons for this: Demand for air travel, and therefore aircraft, is rising, driven primarily by emerging markets and the United States. Moreover, the emphasis on using lightweight materials for better fuel efficiency and specialized joining techniques are necessary for these lightweight rivet materials. These are in great demand and will continue to be so.
Conclusion
In the aviation industry, rivets play a surprisingly pivotal role.
These tiny but mighty components are critical to ensuring the aircraft's structural integrity, which is essential to every flight's safety and reliability. Rivets excel in distributing the enormous stresses an airplane endures, from the force of takeoff to the pressures at cruising altitude and even in the unpredictable turbulence that can occur.
They are uniquely suited to handle the substantial temperature variations experienced during flight cycles, ensuring the joint remains intact and robust despite the thermal challenges.
Moreover, riveting as a method has stood the test of time in the manufacturing process, offering unmatched efficiency and a high degree of reliability. Its simplicity allows for quick assembly and straightforward maintenance, contributing significantly to the aircraft's overall operational efficacy.
Also read:
Planenerd Newsletter
Join the newsletter to receive the latest updates in your inbox.